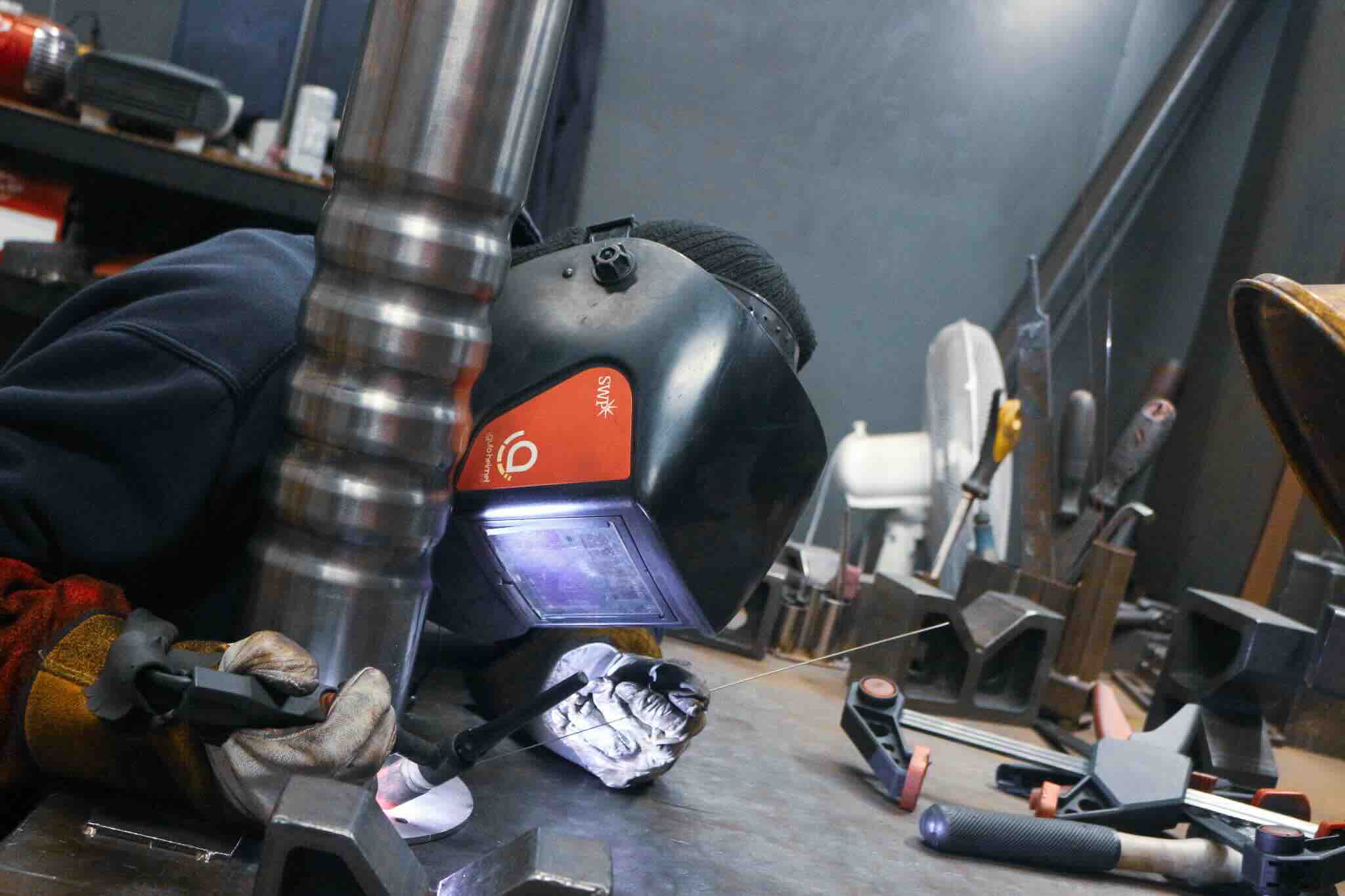
TIG Welding
TIG welding, renowned as Tungsten Inert Gas welding, emerges as the pinnacle of metal fusion techniques, captivating both novice enthusiasts and seasoned professionals with its finesse and precision. Envision a scene where a steadfast hand meticulously guides a slender tungsten electrode, enveloped in a protective argon gas shield, delicately traversing metal surfaces. This dance of controlled energy ignites sparks that weave an intricate tapestry of strength and precision, exemplifying the essence of TIG welding.
What distinguishes TIG welding is its unparalleled versatility and meticulous attention to detail. Capable of welding an extensive range of metals, from delicate aluminium sheets to robust stainless steel plates, TIG welding proves its efficacy across diverse applications. Characterised by its low heat input and precise control, the process ensures impeccable welds with minimal distortion. It is the preferred choice for projects necessitating the utmost precision and aesthetic appeal.
Tig welds demand adeptness, patience and dedication to master the complexities of electrode manipulation and weld puddle control. From critical aerospace components to intricate sculptures, TIG welding ensures excellence in metalworking. A successful Tig weld is a testament to the welder's skill, commitment, and passion.
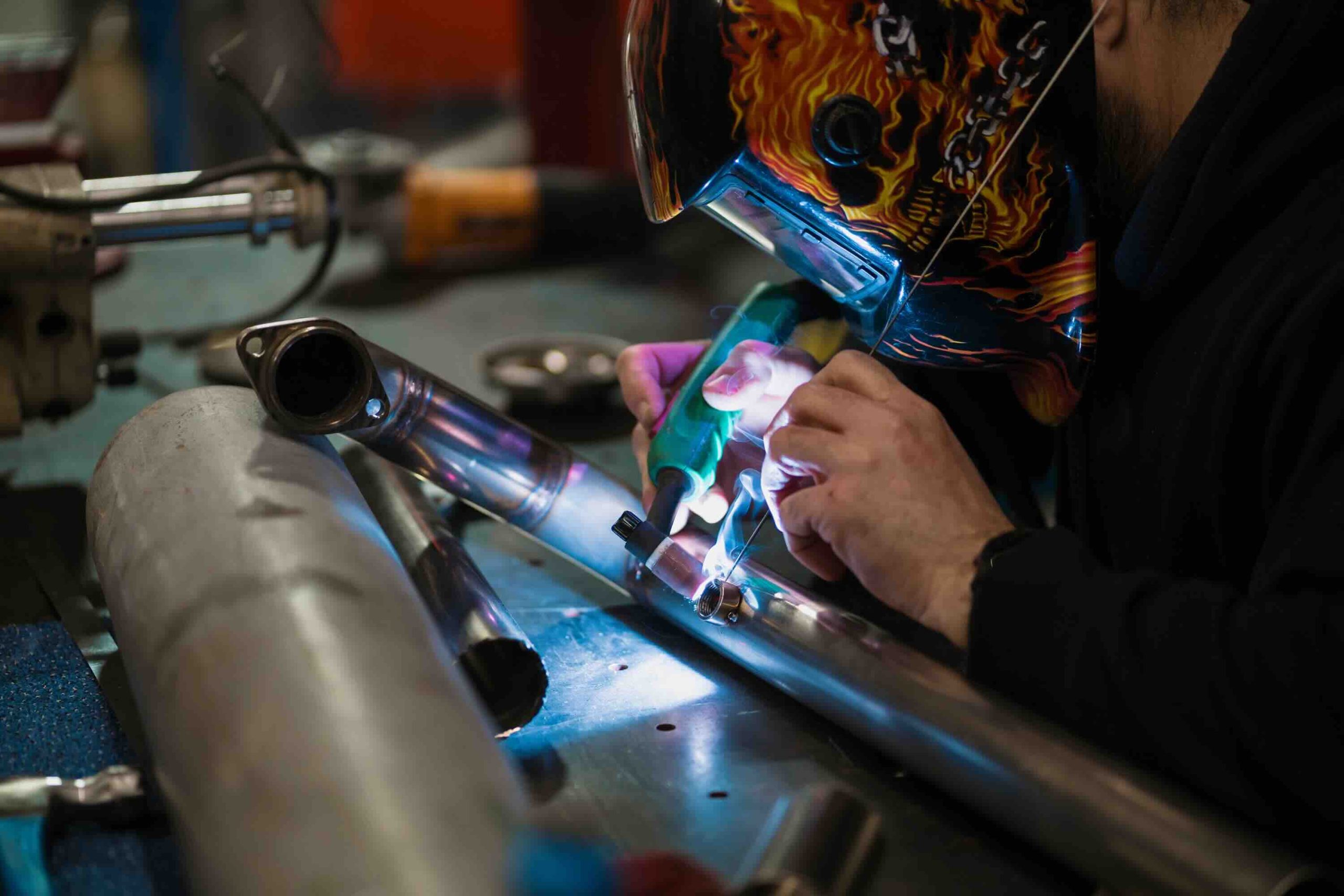
MIG Welding
MIG welding, also known as Metal Inert Gas welding or Gas Metal Arc Welding (GMAW), is a cornerstone of metal fabrication. This method combines precision, power, and skill, transforming raw metal into expertly welded creations.
What sets MIG welding apart is its efficiency and versatility. By continuously feeding wire and using a protective inert gas shield, it seamlessly welds a wide range of metals and thicknesses. Whether working with the strength of steel, the flexibility of aluminum, or the corrosion resistance of stainless steel, MIG welding delivers strong, flawless welds that stand the test of time.
Beyond its technical advantages, MIG welding is accessible and highly efficient. With the right tools and training, practitioners from various backgrounds can master its techniques, unlocking limitless possibilities for creativity and innovation. Whether it’s for automotive repairs or architectural projects, MIG welding offers a fast and reliable solution for all metalworking needs, from large-scale undertakings to smaller tasks.
Brazing
Brazing unites metals without melting them entirely. It’s a process where a lower melting filler material, such as bronze or brass alloy, bridges the gap between metal pieces. This filler material flows into the joints through capillary action, creating a bond stronger than the base metals.
What sets brazing apart is its finesse. Unlike welding, which can be brute force, brazing requires meticulous control of temperature and atmosphere. This precision ensures that the metals bond effectively without compromising their structural integrity. The result? Clean, tidy joints that are nearly invisible, seamlessly integrating into the metalwork around them.
From crafting intricate jewellery to constructing robust machinery, brazing finds its place in a range of industries. Its ability to create strong, durable, and aesthetically pleasing joints makes it a favourite among artisans and engineers.
We are Ready
Giving You The Best Services
Delivering top-notch services tailored to exceed your tube fabrication expectations.
Years Of Experience
For over 30 years, we’ve been delivering expert craftsmanship and industry-leading services.
Projects Completed
With a proven track record of success, we’ve completed over 2,000 projects, each with precision and care.
Our Process
Streamlined steps for guaranteed success:
1.
Design and Planning
2.
Material Selection
3.
Cutting
4.
Bending and Forming
5.
6.
Welding and Joining
End Forming
7.
8.
Machining
Quality Control
Customer Testimonial
“Global Tube Fabrication delivered exceptional quality on our coffee machine tube fabrication project. The parts fit perfectly and significantly improved our machines’ performance. Fast, precise, and reliable service—highly recommended!”
Get Your Custom Tube Fabrication Quote Today!
Ready to bring your project to life? Don’t wait! Our dedicated professionals will review your requirements and provide a competitive quote promptly.